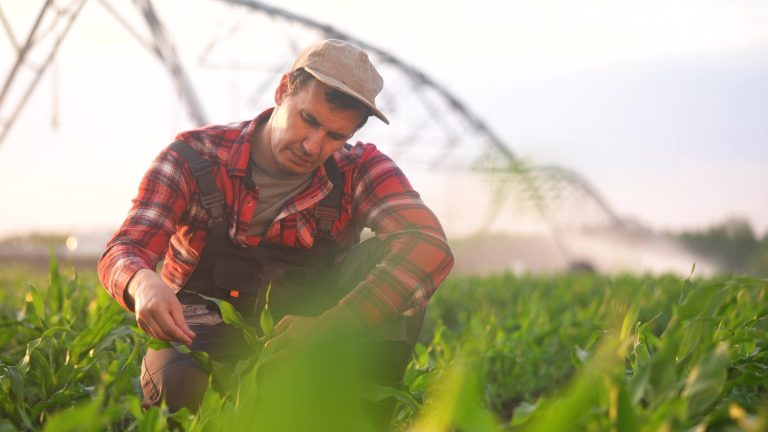
Fenntartható vízgazdálkodási közösség alapítása
Fenntartható vízgazdálkodási (korábban öntözési) közösség létrehozásának ügyintézése, pályázati feltételeknek megfelelően, biztos jogi és szakmai alapokkal.
Fenntartható vízgazdálkodási (korábban öntözési) közösség létrehozásának ügyintézése, pályázati feltételeknek megfelelően, biztos jogi és szakmai alapokkal.
Mezőgazdasági öntözéstervezés és kivitelezés akár kulcsrakész átadásig, jogi, műszaki és pályázati szempontokat is lefedő, komplex projektmenedzsmenttel.
A zökkenőmentes kivitelezéshez és pályázatbenyújtáshoz teljes körű ügyintézés, a szükséges vízjogi és környezetvédelmi engedélyek beszerzése.
A sikeres pályázat benyújtásához szükséges műszaki és adminisztratív támogatás.
Modern öntözőberendezések telepítése minden mezőgazdasági területre. Pontos, víztakarékos, automatizálható megoldások komplex kivitelezése a vízkivételtől a kijuttatásig, költséghatékony megoldással.
Komplex vízjogi és környezetvédelmi engedélyeztetés a beruházás teljes életciklusára, jogszabályi megfeleléssel és szakértői támogatással.
Környezeti hatásvizsgálat és engedélyeztetés a beruházás környezeti megfeleléséhez: vizsgálatok, elemzések, dokumentáció és szakmai támogatás.
Környezeti kockázatok feltárása és kezelése építkezések előtt, engedélyeztetés, szennyezettségi vizsgálat, ökológiai felmérés, szakértői támogatással.
Környezeti monitoring: víz, talaj, üledék mintavétel és elemzés, szabályozási megfelelés igazolása, modellezés és előrejelzések készítése.
Környezetvédelmi támogatás iparvállalatoknak: jogszabályi megfelelés, költséghatékony megoldások, környezetmenedzsment és szakértői tanácsadás.
Teljes körű „egyablakos” szolgáltatás a tervezéstől a kulcsrakész átadásig.
35 éves tapasztalat a vízgazdálkodás és a környezetvédelem területén.
Valamennyi részterületen képzett, tapasztalt szakember gárdával rendelkezünk.
A részfeladatok együttes kezelésével javítjuk a költséghatékonyságot.
Fennállásunk 35 éve alatt Magyarország egyik legismertebb és legelismertebb vízgazdálkodási, természetvédelmi és környezetvédelmi tanácsadó cégévé váltunk. Kulcsterületeink az öntözésfejlesztéshez, vízgazdálkodáshoz, természetvédelemhez és környezetvédelemhez kapcsolódó tervezési és kivitelezési szolgáltatások.
Szolgáltatásaink lefedik a tudományos és műszaki tanácsadást, a mérnöki tervezést, valamint a projektek előkészítésétől a megvalósításig terjedő folyamatok menedzselését és végrehajtását. Akkreditált mintavételi csoportunk korszerű eszközökkel végzi a terepi vizsgálatokat megbízóink számára.
Csapatunk mindig készen áll, hogy segítsen vízgazdálkodási, természetvédelmi és környezetvédelmi kérdésekben. Kérdéseivel forduljon hozzánk bizalommal.